

We then use the captured speckle patterns to identify the material type with our trained neural network. We built a hardware add-on consisting of a laser pointer and a lensless image sensor, which can be attached to the laser cutter head using a mount. This imaging technique works by pointing a laser onto the material’s surface and imaging the resulting speckle patterns. A material’s surface structure is unique even when it is visually similar to another type. In this paper, we investigate how we can identify laser cutting materials by leveraging one of their inherent properties, i.e., surface structure. These issues exist because using tags for identification is not inherently material-aware as the laser cutter does not measure the physical properties of the material. Second, laser cutter users need to be careful to not cut off the tag to ensure that the remaining part of the sheet can later still be identified.

First, a new tag has to be attached onto each new material sheet. However, scanning the tags to detect the material type has its own issues. As can be seen in Figure 2b, these tags can be detected by a camera even when materials look similar or are transparent. To ensure reliable identification, recent laser cutters use sticker tags attached to the sheets (e.g., QR codes on Glowforge Proofgrade sheets). However, a conventional camera can be easily fooled by visually similar materials or materials with printed decorative textures that imitate another material. One naive solution for this is to add a camera to laser cutters to automatically identify the sheets. īecause of the challenges outlined above, laser cutter users desire smarter machines that can "identify the materials they working with, so that the system could suggest settings based on material" as shown in a recent HCI study by Yildirim et al. These hazardous materials may easily be mistaken for safe materials due to similarity in appearance (e.g., PVC vs. Further, there are many materials that are not safe to laser cut because they release toxic fumes. This can lead to wasted material when the power setting is too low, causing the outline to not be cut through – or worse the material may catch fire when the power is too high leading to safety risks. As a result, users may take the wrong material from the stack and use it with another material’s power and speed setting. įor users, working with the various materials available in a workshop comes with several challenges: First, identifying unlabeled sheets from scrap buckets or material stockpiles in a shared workshop is challenging since many materials are visually similar. While there have been many support tools for laser cutting that help users with tasks such as automatically packing parts onto sheets, systems that support users with the different material types available for laser cutting are largely unexplored. We evaluate SensiCut’s accuracy for different types of materials under different sheet orientations and illumination conditions. In addition to improving the traditional workflow and its safety, SensiCut enables new applications, such as automatically partitioning designs when engraving on multi-material objects or adjusting their geometry based on the kerf of the identified material. SensiCut consists of a compact hardware add-on for laser cutters and a user interface that integrates material sensing into the laser cutting workflow. It achieves this by detecting materials’ surface structures using speckle sensing and deep learning. SensiCut enables material awareness beyond what users are able to see and reliably differentiates among similar-looking types.

To support users, we present SensiCut, an integrated material sensing platform for laser cutters. This can lead to problems, such as using the wrong power/speed settings or accidentally cutting hazardous materials. Laser cutter users face difficulties distinguishing between visually similar materials. (c) Each identified sheet is cut with the correct power and speed settings.
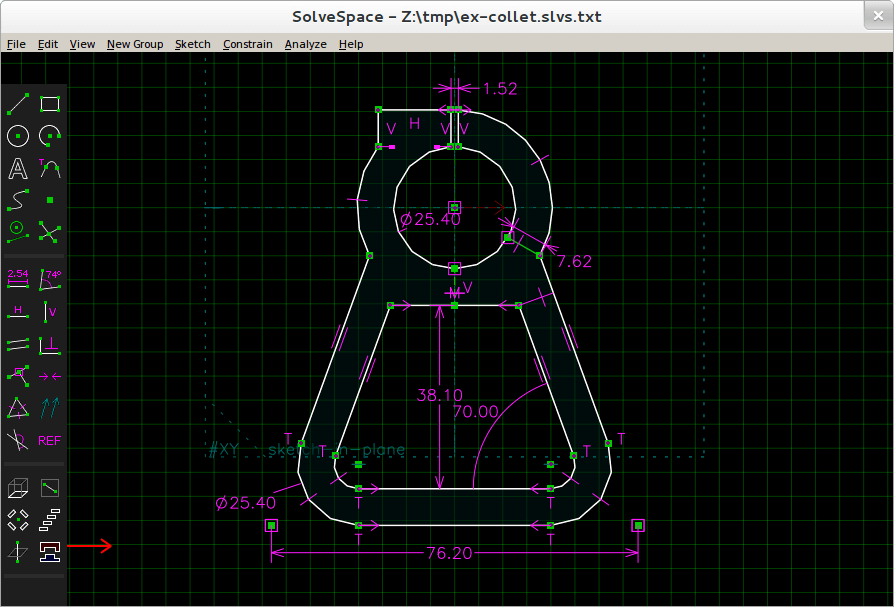
#ENGRAVE A PHOTO ON LASER CUT 6.1 HOW TO#
(b) SensiCut’s user interface integrates material identification into the laser cutting workflow and also offers suggestions on how to adjust a design’s geometry based on the identified material (e.g., adjusting the size of an earring cut from felt since the kerf for felt is larger than for other materials). SensiCut augments standard laser cutters with a speckle sensing add-on that can (a) identify materials often found in workshops, including visually similar ones.
